Drive manufacturers are updating their products to satisfy the changing needs of designer demands. This includes more powerful drives with added functions, better efficiency and better connectivity, among other features.
An on-going trend across industries is that manufacturers are seeing more of a demand for custom products to suit highly specific customer needs and applications. For some drive manufacturers, this takes the shape of working closely with their customers on their designs.
In fact, companies like ABM Drives base much of their business on working closely with customers to develop custom products. As Gabriel Venzin, President of ABM Drives notes, most of their products are engineering in close cooperation with their customers.
Engineers at Lenze see much the same thing and offer a host of specialized services to aide customers. “Lenze offers full application engineering services which include programming assistance, hardware selection, product demonstration, in-house testing and onsite commissioning,” says Kevin Corcoran, Application Engineer with Lenze Americas. “In addition, field service or after sales technical support are available and there is also 24-hour emergency phone support for customers with critical machine stoppages outside of business hours” adds Corcoran.
Another theme is interoperability. More often than not a design sources components from multiple vendors or even sports legacy and newer components from the same vendor, and so the need for all these pieces to work together is critical. So because multiple vendors are involved in a single project, interoperability becomes more important.
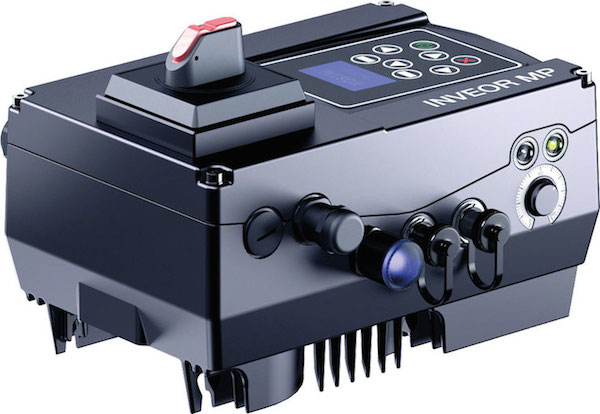
According to Venzin from ABM Drives, the company designs products that can be combined into different end products … and various gearboxes can be equipped with ac induction motors … or Sinochron PMAC motors. Plus the motors can be mounted or used with cabinet-installed inverters — or with no inverter if the design engineer wishes.
The same is true for Lenze. The company “takes several measures to allow for interconnection between our products”, says Corcoran. “The EASY Engineering Tool suite is used to promote simple access to products both legacy and current. Many of our products share similar fieldbuses that allow them to integrate easily into a Lenze PLC or even a 3rd party fieldbus structure.”
What else is driving business for drive manufacturers? For one, both expanding as well as entirely new applications. For instance, ABM Drives reports that they’ve seen more interest for their products across a broad swatch of applications and industries. AGVs (automated guided vehicles) are one area to consider. AGVs and other battery-powered equipment demands increased partly due to labor shortages and include more and more flexible assembly platforms instead of fixed assembly lines. Some vehicles are being converted to electric due to noise concerns allowing operation during night time or weekends or close in noise-sensitive buildings such as hospitals and nursing homes.
Also, applications in automated warehousing (so-called AS/RS systems) are seeing more demand for integrated systems that incorporate Industry 4.0 functions and combine conventional conveyor systems with AGVs. Some other applications like all-terrain vehicles (ATVs) and utility task vehicles (UTVs) have a need for drives, but limited battery life and associated cost still holds back quick expansion in these areas.
As for the future of engineering education and internship or training programs, ABM Drives is actively involved in bringing about the next generation of engineers and tech workers. As a German company ABM has always employed apprentices for functions such as mechatronics and machining. They also provide opportunities for internships for technology students from university programs. In the end, the company strongly believes that training of young professionals for all key functions is a must for long term survival and success of the company.
Leave a Reply
You must be logged in to post a comment.