Slip rings — also called electric swivels, collector rings, and rotary electrical joints — are electromagnetic devices of electromechanical, fiber-optic, or even non-contacting inductance and capacitance subtypes that transmit power and data signals between a rotating machine segment and a stationary segment.
Of course, power transmission is associated with higher voltage and higher current than that of data transmission via slip rings. That transmission of power can be for applications needing high voltage, dc, or ac power.
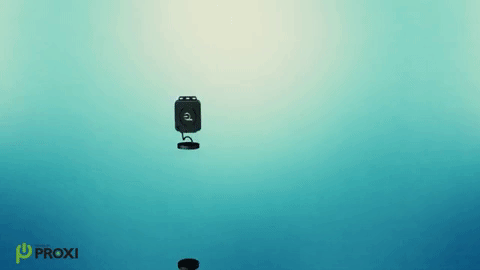
To be clear, the original slip-ring application was to transmit power. But today’s slip rings can transmit analog as well as digital signals from feedback devices … and even data via Ethernet or industrial fieldbuses.
Regarding electrical power through a slip ring — where does it go?
In many cases, the electrical power goes onward to drive electric motors, solenoids to trigger the action of hydraulics, or other electrically-driven actuators.
How do the signals through a slip ring get used?
Transmission of data signals can be that for controls, sensors and strain gauges of various types, audio and video, and digital information … often to support IoT and preventative-maintenance functions. In fact, many manufacturers further subcategorize these slip-ring functions for control and for data transmission, as their requirements often differ. The frequency of data signals can vary — from a straight dc signal to GHz … with the highest frequencies and fastest speeds requiring sophisticated slip-ring designs.
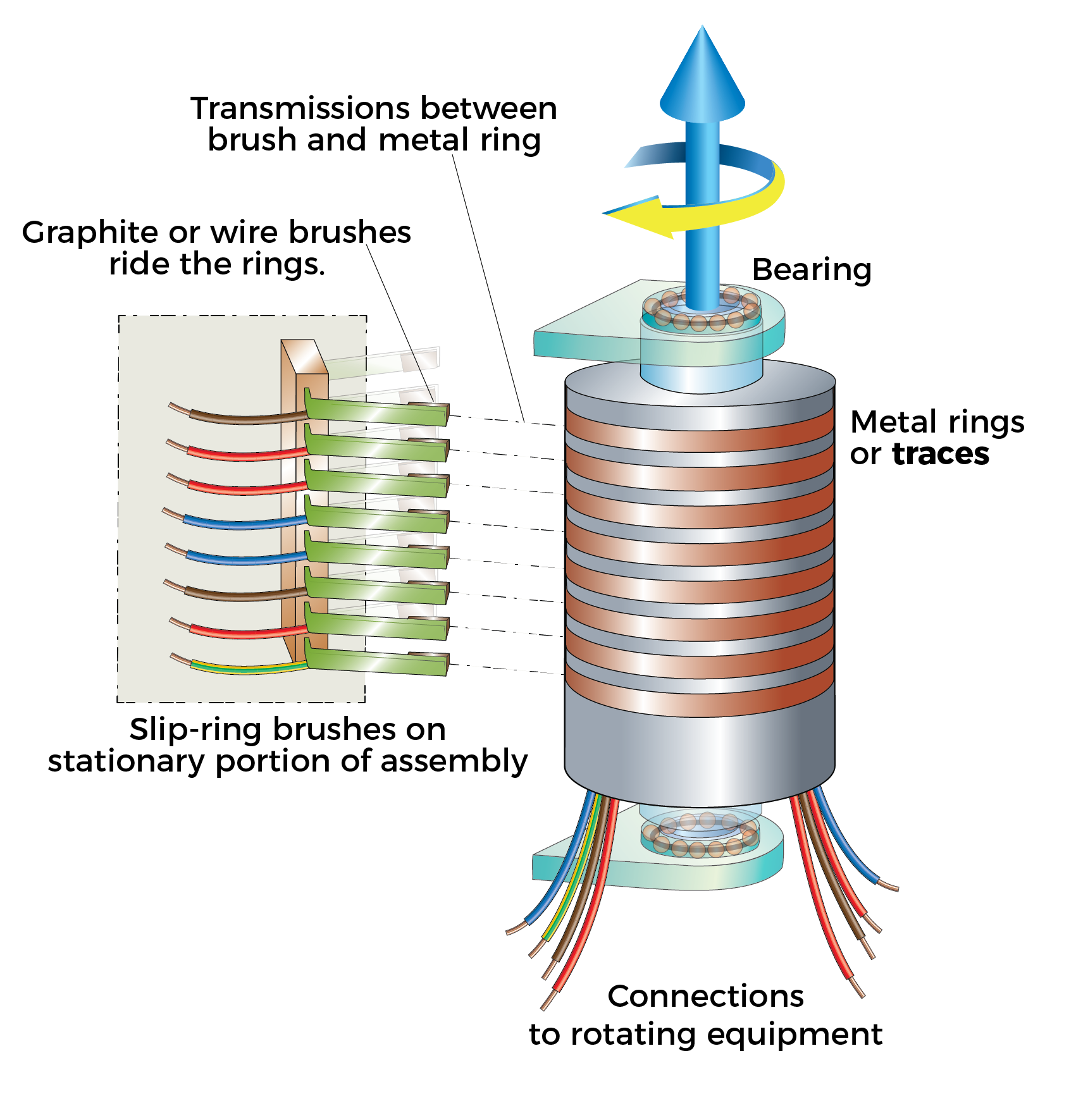
Adding such functionality means slip rings enable unique applications that would otherwise be impossible … or at least streamline mechanical designs while avoiding the use of wires at moving joints. They’re most common in wind turbine, medical, aerospace, marine, and industrial applications.
Of course, if a machine assembly includes the rotation of one section with a fixed number of revolutions, it may be possible to use spools with sufficient cable length and rotating speed to allow for the required revolutions …
But if a machine section continuously rotates, it’s not particularly practical or reliable to use cables to transmit signals between the rotating and stationary sections.
A webinar on this topic was presented live on Tuesday, December 18, 2018. Click below to watch it on demand.
Not to say that slip rings don’t work in applications needing less than 360° of swiveling or oscillating. In fact, limited-stroke rotary axes are quite common. One consideration here is that the slip ring include feature for clockwise and counterclockwise rotation.
This is a stellar example from California-based motion-control manufacturer Newmark Systems …
Slip rings do contain wear elements beyond the sliding-element brushes and conductor rings (in the case of electromechanical variations) in the form of ball bearings. Lubrication with grease packing eliminates the need for maintenance but isn’t always suitable for environments with extreme pressures or temperatures.
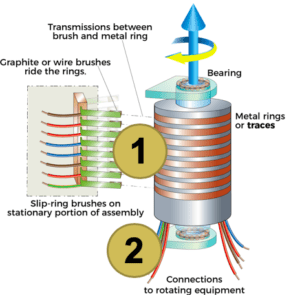
In some cases, external lubrication and even thermocouples are employed to ensure long life and top speeds while tracking any overheating of the bearing elements.
Are there any technologies that compete with slip rings?
Yes … for data communications in particular, there are wireless connections to transmit from moving machine sections to those that are stationary. Here, such options can outperform legacy slip rings and those out of service and exhibiting signal jitter and degradation from excessive vibration, for example.
Of course, Wi-Fi, infrared, and radio-based communications can have their own issues — as anyone who’s struggled with a Bluetooth-enabled device can attest. But these may be options for some environments and select applications with certain electromagnetic compatibility (EMC) requirements … as well as those needing remote monitoring and certain data throughputs.
Of course, wireless slip-ring technologies for both data and power blur the lines between these applications and definitions relating to slip rings and other technologies.
Leave a Reply
You must be logged in to post a comment.