Smart manufacturing, battery production, and the packaging industry all benefit from realtime and deterministic communications.
Lisa Eitel • Executive editor | Design World
Thomas Burke • Global Strategic Advisor | CC Link Partner Association (CLPA)
Realtime and deterministic communications based on Ethernet have become essential to modern-day discrete automation. Now, all major industrial network protocols either have intrinsic realtime determinism or have incorporated time-sensitive networking or TSN.
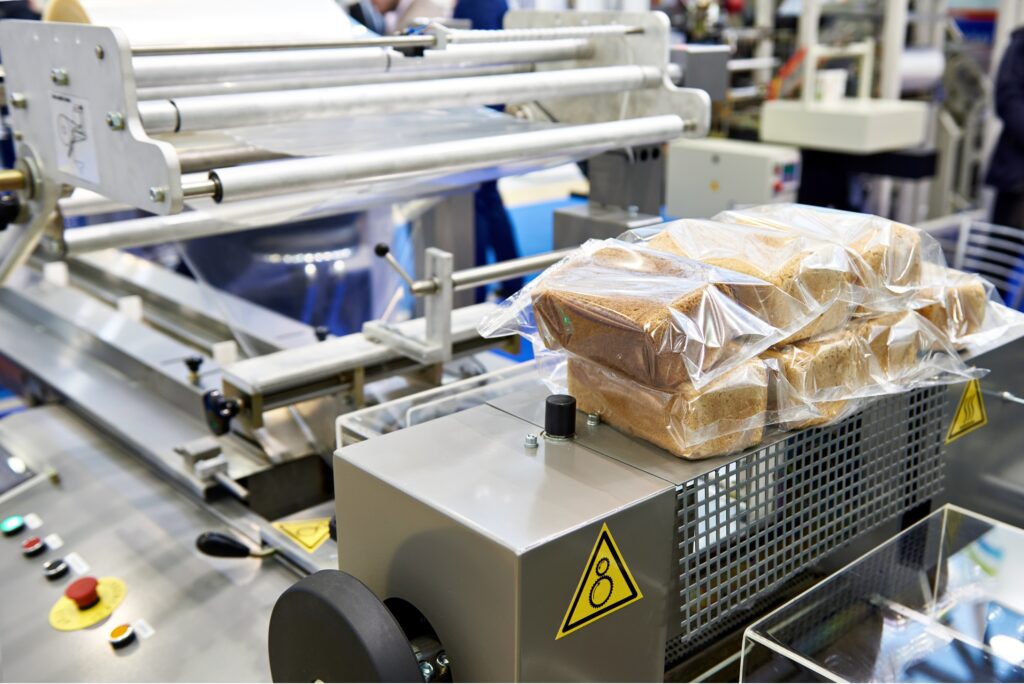
In short, TSN prioritizes and schedules data to arrive precisely sans delay — a core capability for the proper operation of precision robotics and the motion-control systems of automated equipment. TSN renders standard Ethernet deterministic at the so-called Layer 2 Open Systems Interconnection Data Link reference model. That in turn lets multiple traffic types share a given network — a key trait of equipment and operations to satisfy digital transformation (DX) objectives.

Putting CC-Link in context
The open protocol known as Control and Communication Link — CC-Link — is a leading global standard to connect devices in manufacturing settings. It’s designed to enable deterministic communication between industrial controllers, robots, and multi-axis machinery.
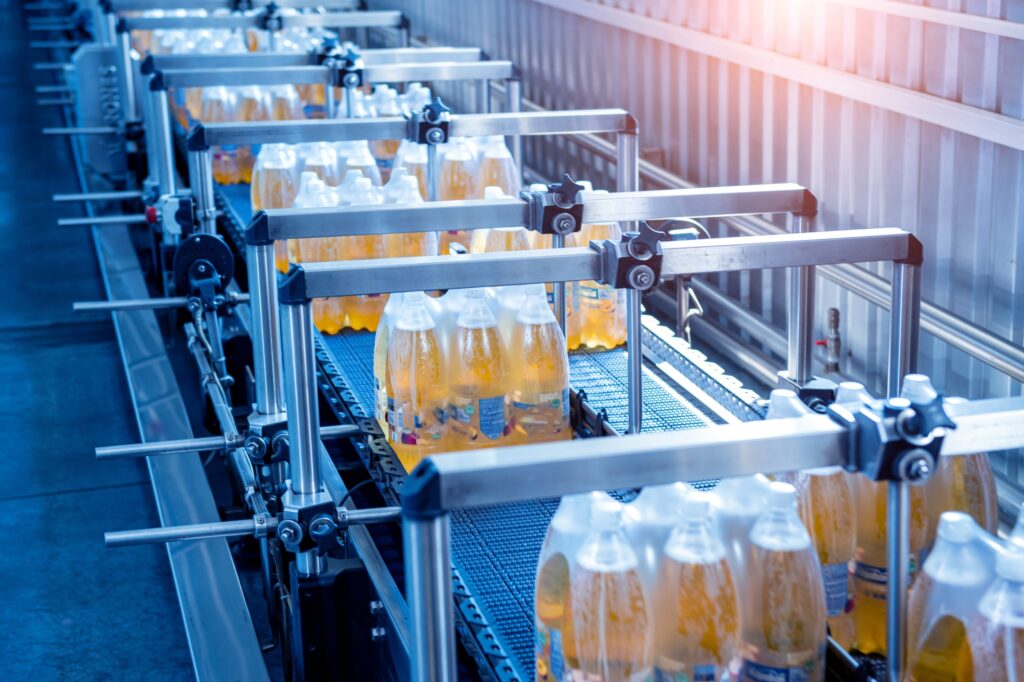
CC-Link IE TSN combines CC-Link’s reliability with the realtime features of TSN to handle standard Ethernet traffic and realtime control data on one network. With TSN, the exact time data needs to travel the network as well as any delays (latency) and travel-time variations (jitter) are fully defined, managed, and minimized. This allows use of CC-Link IE TSN in even the most sophisticated machine applications.

Time-sensitive networking in smart manufacturing
Digital manufacturing, also called smart manufacturing, has spurred the convergence of software and cloud computing for traditional machining, additive manufacturing, and injection molding. The use of digital twins has become an integral part of new product design, manufacturing process planning and improvement, predictive maintenance, RFQ/RFP, and capacity-utilization analysis.

Digital twins often simulate physical processes. When engineers make changes on these digital twins before implementing changes on physical processes, they can identify potential bottlenecks or limitations that may be encountered — in turn reducing production losses and the degradation of quality.
Digital twins rely on extensive real-world machine data to create machine models. Choosing more capable industrial communications — for example, those based on Gigabit Ethernet with TSN — essentially boosts the collection of data. That in turn leads to more accurate and complete simulations.

Time-sensitive networking in battery production
North American EV battery production has benefitted from governmental efforts to increase U.S and Canadian competitiveness. Now automation systems are being used in new ways for this specialized market.
Especially for the U.S. automotive industry, batteries are an important part of the overall EV value chain. The closer these batteries can be created to the end use (automotive manufacturing) the better for supply chain management and product-quality risk management.

While the machines used for actual production are typically supplied by international sources, their purchase and integration into American manufacturing operations must be fast and simple. Challenging is how these machines are very complex in design and operation and include a significant focus on motion control — especially for winding tasks. Such tasks require high-performance motion coordination.
Leading technology in this area is one automation-component supplier’s CC-Link IE TSN protocol that connects controllers and servo amplifiers with nsec responsiveness. The result is an advanced lithium-ion battery (LiB) production machine that can deliver high performance, flexibility, and sensor and camera connectivity to improve overall throughput.
Time-sensitive networking in the packaging industry
The packaging industry has undergone a slow revolution in recent decades, and has been influenced by the machine designs of certain OEM vendors. Today, molding workcells, printing machines, cartoning equipment, case-packers, and palletizers have become smart machines. Here, Ethernet with TSN has enabled the coexistence of OT and IT communications on the same backbone, simplifying architectures and reducing costs. In this context, smart means these machines are capable of data collection, machine diagnostics, high-quality performance monitoring, and precision control.

Of course, all these capabilities necessitate increased data access, improved sensors, and more flexible technologies capable of prompting operation step-changes. Ethernet with TSN as a machinery communications backbone and TSN-supporting vendors have made scheduled and prioritized communications on Gigabit Ethernet possible to support these smart functions.
CC Link Partner Association (CLPA) | cc-link.org

Leave a Reply
You must be logged in to post a comment.